Центробежное литье в силиконовые формы
Центробежное литьё в силиконовые пресс – формы – это наиболее простой, с технологической точки зрения, способ тиражирования моделей из сплавов с температурой плавления до 500 градусов, полиуретановых и эпоксидных смол.
Технология центробежного литья широко применяется во всём мире для изготовления сувенирной продукции бижутерии, рыболовной оснастки, мебельной и текстильной фурнитуры, наградной продукции и технических изделий. Идеально подходит для производства от 100 до 3000 изделий за рабочую смену. Центробежные литейные установки бывают нескольких типов и классифицируются по их диаметру. Наиболее популярные из них – однопозиционные, диаметром формы от 300 до 400 мм, полный цикл для одной пресс – формы, в которых составляет 1-2 минут.

Исходя из геометрии, массы, детализации, отливаемых изделий и используемого сплава подбирается наиболее оптимальная для литья формовочная резина. В зависимости от выбранного сплава срок жизни пресс – формы варьируется от 100 до 2000 циклов литья.
1 этап – Прототипирование:
Для начала необходимо изготовить мастер – модель. В качестве моделей обычно используются уже готовые изделия или модели, напечатанные на фотополимерном 3D принтере специальной термоформовочной смолой. В случае, если для моделирования используется воск, модельный или светоотверждаемый пластик, для формовки применяется резина с пониженной температурой запекания (+80 С).
2 этап – Формовка:
Формовка – это самый важный и деликатный этап, в котором на 70% определяется метрическое соответствие отливок моделям и качество готовой продукции. Готовая пресс – форма состоит из двух частей - верхней и нижней. На дно обоймы для вулканизации укладывается первый слой формы, в который по периферии утапливаются (вминаются) подготовленные модели. Расстояние между моделями и до края формы должно быть не менее 8 мм. После размещения моделей поверхность обрабатывается тальком, затем в ней формируются металлические направляющие для точного совмещения с верхним слоем формы.

Сверху этот пирог накрывается вторым слоем резины, формируется центральная горловина, куда будет поступать металл и плотно закрывается крышкой. Обойма помещается в вулканизатор на 30 – 120 минут, в зависимости от выбранной резины и толщины пресс - формы. После запекания в нижней части пресс - формы прорезается литниковая система и выпоры.
3 этап – Литьё:
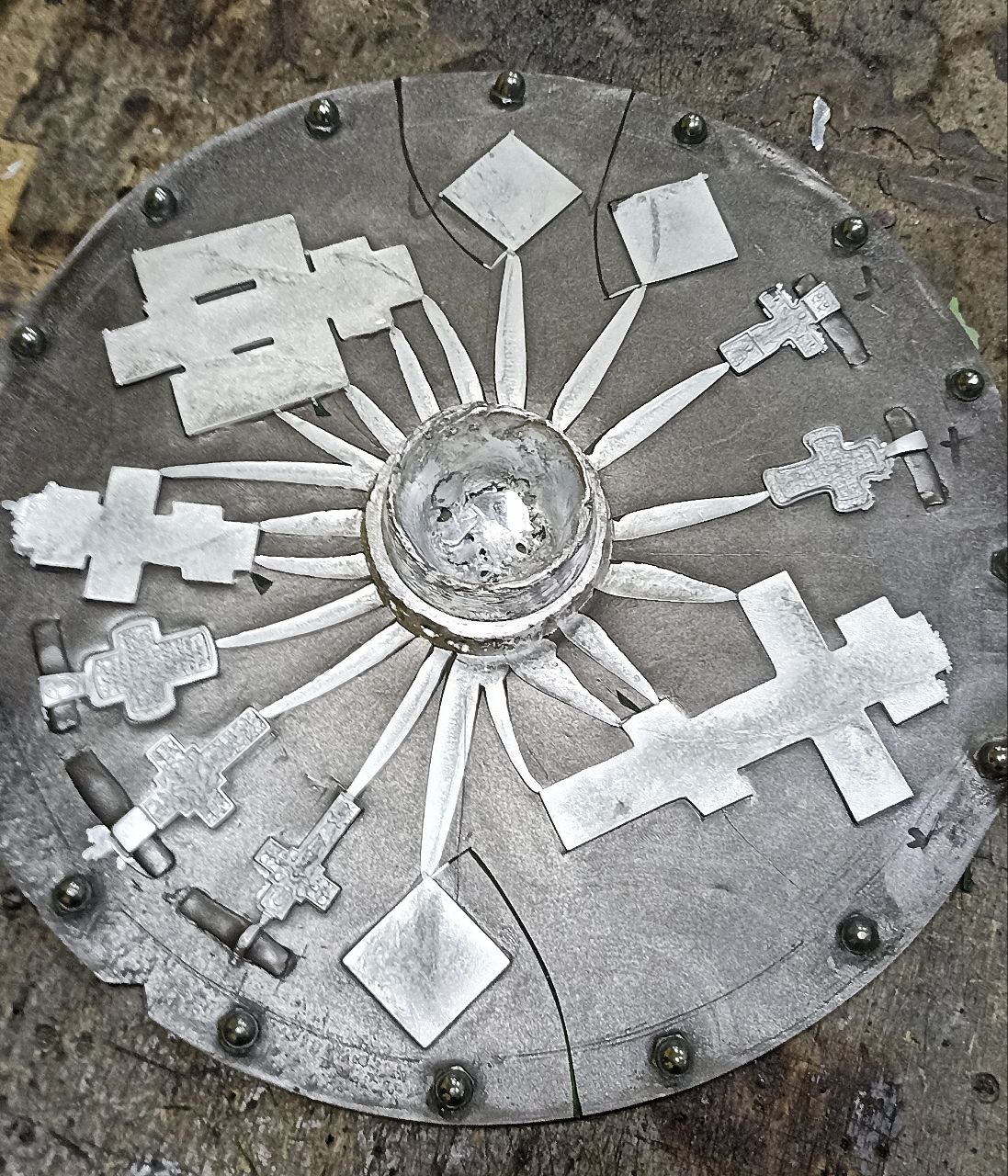
В однопозиционных литейных машинах металл заливается оператором сверху через специальное отверстие в крышке машины и через центральный литник разливается по всем полостям формы, которая при вращении прижимается специальным механизмом. Скорость и время вращения задаётся заранее по средствам цифрового контроллера на передней панели установки. В соответствии с массой и размером изделий подбирается такая скорость вращения пресс – формы, при которой давление, создаваемое центробежной силой, не будет слишком большим, и в то же время будет достаточным для пролива всех рабочих полостей.
От правильного выбора оборотов зависит качество литья. При правильном балансе массы отливок и скорости вращения формы достигается наименьшая усадка металла и отсутствие облоя на отливках. Цикл литья для металлов составляет 1 - 2 минуты, для полиуретановых и эпоксидных смол 5 – 10 минут для одной пресс - формы. По окончании изделия отламываются от литников, после чего они готовы для дальнейшей обработки.